A dead-end clamp, often called an anchor or tension clamp, is a hardware fitting designed to terminate and hold cables in overhead line systems securely. They are critical components used in power transmission and communication lines, primarily for securing conductors within the line, bearing tension, and attaching conductors to supporting structures such as towers or utility poles. This guide will provide a full overview of the problem with dead-end clamps, analyzing and presenting it from multiple perspectives, as well as our company’s dead-end clamp products.
It strives to provide you with a comprehensive and clear overview of dead-end clamps so that you can select the best one for your needs.
What's A Dead End Clamp?
First, let’s introduce what a dead-end clamp is. A preliminary understanding of this component will help build context for its functionality from multiple perspectives.
A dead-end clamp, sometimes referred to as a dead clamp, is a mechanical component used extensively in the power industry, particularly in power lines, distribution systems, and telecommunication infrastructure. Its primary role is to provide secure mechanical anchoring by fastening the ends of wires or conductors to utility poles, towers, or other support structures. This ensures the safe, stable operation of the cables under varying environmental and mechanical loads.
To meet the stringent safety, reliability, and durability requirements of electrical systems, the clamp features a compact and slender design. It is typically made from corrosion-resistant aluminum alloy casting, which not only provides the necessary mechanical strength to withstand high cable tension during operation but also ensures electrical conductivity, helping reduce energy loss and maintain efficient current transmission.
The wedge inside the clamp is constructed using weather-resistant and UV-resistant insulating materials, effectively preventing current leakage and potential short circuits. The hoop is usually made from flexible, corrosion-resistant stainless steel or steel wire, enhancing the overall system stability and extending the dead-end clamp’s service life.
These three key structural components—the body, wedge, and hoop—directly influence the total performance of the clamp. Therefore, when selecting a dead-end clamp for use in power lines, particular attention should be given to the materials and performance characteristics of each part.
What is the Dead-End Clamp Assembly?
Dead end clamps consist of multiple components, each playing a crucial role in securing the conductor. Understanding these parts can help in selecting the right cable dead end clamp for specific applications.
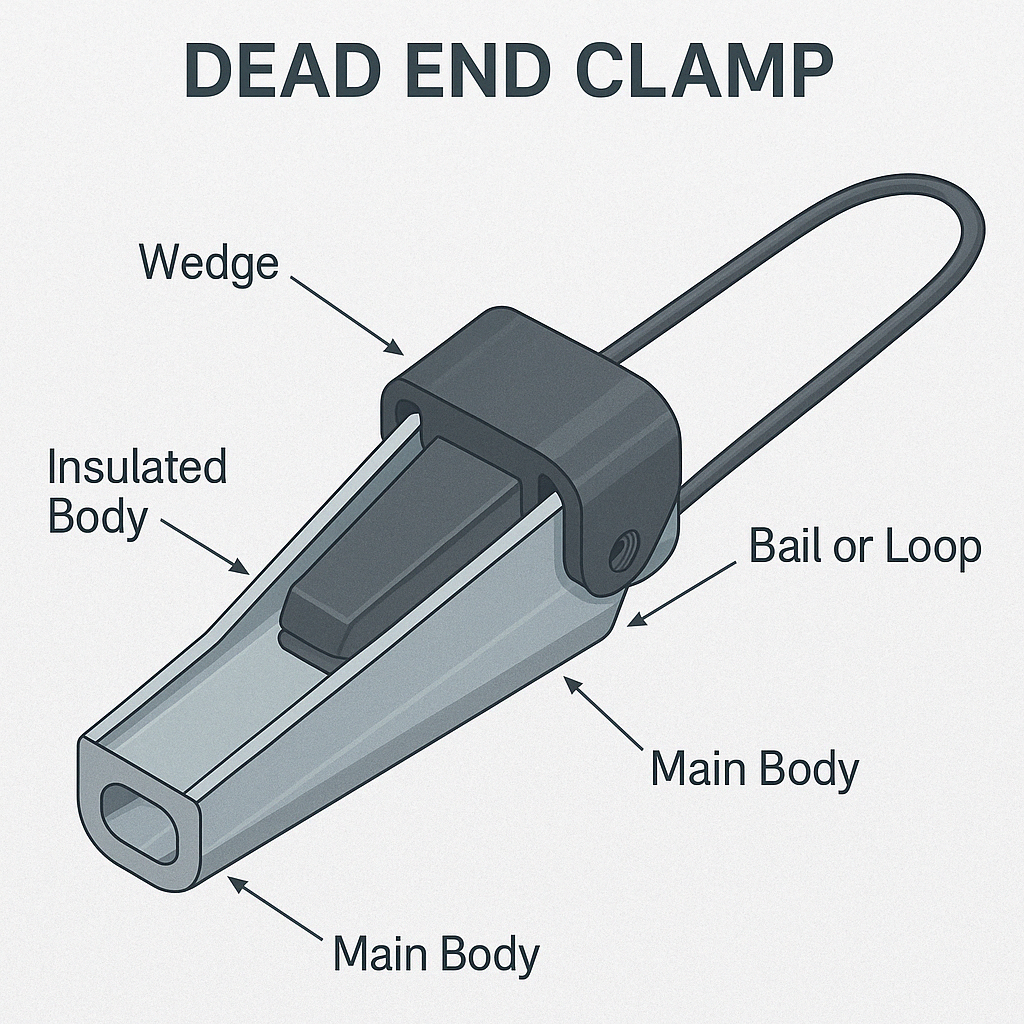
Dead end clamp Structure
Main Components:
- Main Clamp Body: Typically made from high-strength aluminum alloy to provide mechanical support.
- Wedge: Composed of UV-resistant insulating plastic, ensuring cable stability and insulation.
- Bail Loop or Clevis Pin: Made of stainless steel or galvanized steel, providing secure anchoring.
- Stirrup (for certain models): Allows better adaptability for specific conductor sizes.
- Bolts & Nuts: Used to firmly secure the clamp to the conductor and support structure.
Each part is designed to work together, ensuring the dead end clamp for ABC cable provides long-term stability and safety.
How Do Dead End Clamps Work?
The primary function of a dead end clamp is to grip, support, and anchor conductors. These clamps apply mechanical tension to prevent cables from loosening or breaking under stress.
Operational Process:
Cable Insertion: The conductor is inserted into the clamp’s groove.
Tensioning Mechanism: The wedge system ensures a firm grip on the cable, preventing movement.
Load Bearing: The clamp resists mechanical loads, minimizing conductor sag.
Electrical Transmission: Conductors made of aluminum or copper alloy allow smooth energy flow.
Adjustable Fit: Bolts and nuts help secure the clamp while allowing slight adjustments based on conductor size.
Dead clamps are designed to provide long-term stability and prevent conductor slippage or excessive strain in overhead line systems.
Dead End Clamp Function
Dead end clamps perform multiple critical functions in power and communication line installations. Their main roles include:
1. Mechanical Anchoring
Securely fix the terminal ends of conductors to poles or towers, preventing slippage, sagging, or accidental disconnection under tension or environmental stress.
2. Sealing Protection
Provide a tight seal to protect cable ends from dust, moisture, and other contaminants. This ensures long-term stability and prevents degradation of the cable insulation.
3. Electrical Insulation
Integrated insulating components prevent contact between live conductors and grounded parts, reducing the risk of short circuits and improving system safety.
4. Stress Relief
Effectively absorb and redistribute mechanical stress during installation or operation, especially under wind load, thermal expansion, or vibrations—helping to protect cable integrity.
5. Environmental Durability
Designed to resist UV radiation, corrosion, extreme temperatures, and harsh outdoor conditions—ideal for long-term, maintenance-free performance.
6. Easy Installation & Maintenance
Application-specific designs allow for fast and straightforward installation. Some models even enable routine inspection or replacement without dismantling the full system.
7. Compatibility with AB Cables and Poles
Widely used with aerial bundled cables (ABC) and standard pole systems, making them suitable for urban and rural distribution networks.
8. Variety of Sizes & Designs
Available in multiple sizes, shapes, and tension ratings to suit different cable types, voltage levels, and installation conditions.
Dead End Clamps In Different Applications
Insulated Dead End Clamps: These clamps can provide insulation to prevent electrical leakage and shock. They are commonly utilized in lines with insulation requirements to provide reliable transmission over the whole line.
High-voltage Dead End Clamp: The name indicates that this type of clamp is intended for high-voltage applications. It can endure extremely high voltages and continue to function properly, ensuring the wire’s stability. It typically has an insulating layer to enhance safety.
Wedge-shaped Clamp: Typically, the wire is secured by a wedge-shaped design, allowing the clamp and wire to be firmly fixed. It is mostly used to repair low- and medium-voltage cables.
Spiral Pre-twisted wire clamp: This type of clamp is often used for optical fiber and communication lines, and it provides a uniform grip on the cable by spiral wrapping.
Secure your operations with IEC and ISO-approved electrical fittings— Contact us for a sample!
Bolt-type Clamp: It is also an adjustable clamp. To assure the wire’s stability, the clamp’s bolts can be changed to meet actual use requirements. It can be used on lines of varying specs.
Pull-type Clamps are normally built of high-strength materials, can bear high wire strain, and ensure that the wire is securely fastened to the tower or pole. It is designed for high-voltage overhead lines.
The usage scenarios and types of cables or conductors vary, so our choice of cable clamps will also differ. We need to select the appropriate ones based on specific situations to ensure the stability of the circuit. For instance, if high tensile strength is required, we must consider the materials, tensile strength, durability, etc., when choosing cable clamps. If you have any other questions about purchasing cable clamps, you can email our experts for the best solutions.
How to Testing of Dead End Clamps
To ensure reliability, dead end clamps undergo rigorous mechanical and electrical testing.
Common Testing Standards:
Tensile Strength Test: Evaluates maximum load-bearing capacity.
Conductor Slip Test: Ensures conductors remain securely clamped.
Salt Spray Corrosion Test (ASTM B117): Tests resistance to moisture and rust.
UV Exposure & Weathering Test (IEC 61284): Ensures performance under extreme sunlight.
Torque Load Test (NF C33-041): Validates fastening strength under repeated use.
Reliable cable dead end clamps meet or exceed these industry standards to ensure performance and durability.
The Importance Of Dead End Clamps
The use of dead end tension clamps has significantly enhanced cable connection and fixation, reducing cable movement or vibration and ensuring line stability. This is critical for maintaining the integrity of the cable system, which plays an important role in electrical systems. Dead End Clamps are also critical for guaranteeing the durability and safety of overhead wire systems. When exposed to external interference without the use of clamps for fixation, overhead wires may encounter loose connections, excessive sagging, and even cable breakage, resulting in system failures, inability to work normally, and losses.
In addition, dead end clamps are made of high-strength materials such as aluminum alloys, and can still ensure their stability and tensile strength in harsh environments such as storms, heavy snow, and exposure to the sun. Frequent inspection and maintenance are not required, which greatly reduces the operating and maintenance costs of the entire system.
Installation And Maintenance Of Dead End Clamps
If you want the dead end clamp to play its duty properly and stably, and to ensure its service life, the correct installation processes and subsequent maintenance inspections are important.
Preparation: This is a necessary step before beginning anything. First, gather the necessary equipment for installation and the clamps we will use, and ensure that the clamps satisfy the required size and requirements.
Open the tension clamp: Remove the tension clamp and unfold the structure.
Set at the end of the line: Insert the cable conductor to be fixed into the designated location of the dead end clamp and set it at one end of the line.
Clamp the wire: Using pliers, clamp the wire into the tension clamp to ensure that it is well fastened.
Fix the upper end: When the cable and the clamp are fixed, use appropriate tools (such as a winch or wrench) to tighten the upper cable to ensure that the clamp applies appropriate tension.
Inspection and maintenance: Ensure that there is good electrical contact between the contact surface of the wire and the clamp, and regularly check the clamp for signs of wear, corrosion or damage. For worn and fixed clamps, we should replace them in time to ensure the reliability and safety of the system.
Application Of Dead End Clamps
Dead End Clamps are widely employed in many sectors and areas, primarily including:
Power transmission and distribution lines: mainly cables fixed in low-voltage and medium-voltage overhead lines.
Communication line: In the communication line, dead end Clamp is used to fix the optical cable or cable on the pole or other supporting structures to protect the optical cable or cable from being affected by tension and external forces.
Railway catenary: In the railway catenary, dead end Clamp is used to fix the contact wire on the pillar, bear the tension of the contact wire, and ensure the stable position of the contact wire.
Insulated overhead lines: Cables used to fix overhead lines, providing reliable fixation and insulation.
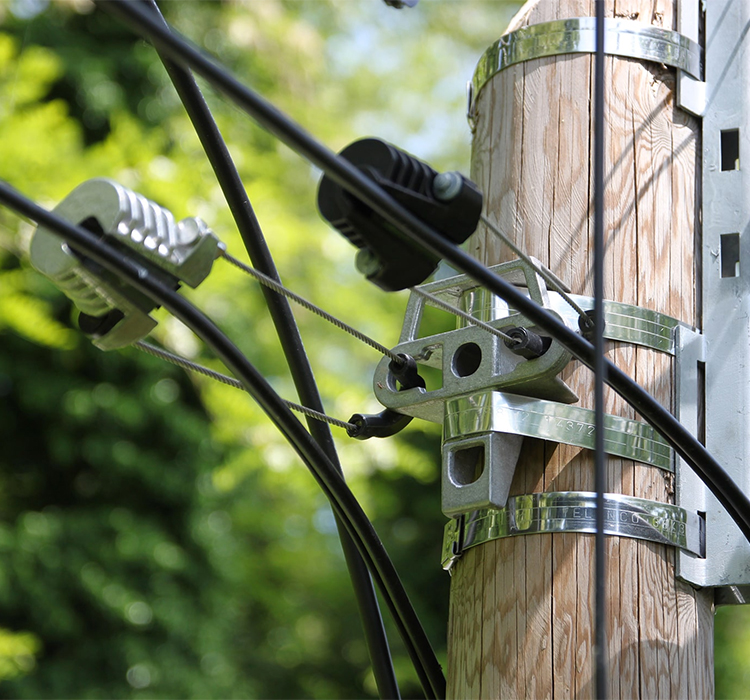
Dead End Clamp Application and Installation
How To Choose the Right Dead End Clamp
Choosing the right Dead-end Camp isn’t just technical box-ticking – it’s about keeping your power lines secure for decades. Let’s break down what really matters:
Match Your Cables
First things first: Check that the clamp plays nice with your specific cable type. Whether you’re working with AAC, ACSR, or ABC cables, that compatibility sticker matters more than you think.
Strength Isn’t Optional
These clamps are your system’s backbone. For heavy-duty jobs (think 44,480N+ loads), you’ll want clamps that laugh in the face of tension. No compromises here.
Materials That Outlast the Elements
Coastal project? Extreme weather zone? Your clamp needs armor. Look for:
Aircraft-grade aluminum alloys
Hot-dip galvanized steel
UV-baked polymers
Bonus points if they’ve survived ASTM B117 salt spray torture tests.
Installation Smarts
Pro tip: Wedge-style clamps with self-locking mechanisms can shave hours off your install time. Less tool-fumbling, more getting-the-job-done.
Certifications Are Your Safety Net
Spot these badges of honor: IEC 61284, IEEE C135, NF C33-041. They’re not just acronyms – they’re your guarantee against nasty surprises.
Why This All Matters
The right cable dead-end clamp isn’t just a purchase – it’s insurance against downtime, safety headaches, and those 3 AM emergency callouts.
Development Trends of Dead End Clamp
As society progresses and science and technology advance, the demand for electricity and communications grows, and dead end tension clamps are constantly updated in terms of materials and designs to meet the needs of modern power systems and fiber-optic communication. As material science advances, the development trend of dead end clamp may become more corrosion-resistant, high-insulation, and strong tensile strength, while the overall weight will tend to be smaller, reducing the overall load of the cable system.In overhead lines, the design of clamp will also tend to be more simplified, ensuring convenient installation, easy replacement and maintenance, while ensuring the durability of the clamp, and ensuring that they can have a longer service life under various climatic conditions, without the need for frequent replacement, reducing safety hazards and reducing costs.
Dead End Clamps From SUNJ
SUNJ Dead-End Clamps: Engineered for Reliability Since 2009
As a trusted ISO 9001/14001-certified manufacturer specializing in overhead line systems, SUNJ delivers precision dead-end clamps trusted by utilities and telecom operators globally. Here’s why professionals choose our solutions:
Core Advantages
Military-Grade Durability
Clamp bodies forged from aerospace-grade aluminum alloy withstand 44,480N+ tensile loads, corrosive environments, and extreme temperature swings (-40°C to +80°C).
Smart Safety Design
UV-stabilized polymer wedges enable live-line installation while preventing galvanic corrosion – critical for coastal/high-salinity areas.
Standards-Driven Performance
Third-party validated to IEC 61284, NFC 33042, and IEC 61238 for guaranteed electrical stability and <0.5% annual maintenance rates.
Conclusion
Dead End Clamps are a useful power accessory. Wire clamp specifications and models vary depending on the usage scenario. When purchasing dead end clamps to maintain line stability and safety, we may use this guidance to make acceptable purchases based on functioning principles, application scenarios, installation and maintenance requirements, and so on. At the same time, you can contact with SUNJ’s professionals to ensure you get the proper dead end clamps. Regardless of the scenario, SUNJ’s products can provide system stability.