Pin type insulators are essential components in electrical transmission systems, providing both mechanical support and electrical insulation to power lines. These insulators ensure the safety and reliability of electrical systems, particularly in electrical power transmission networks. In this blog, we will explore the advantages and disadvantages of pin type insulators, as well as the causes of failure, common standards, and when to use them.
1. Introduction
Pin type insulators are widely used in electrical systems to secure electrical conductors to overhead lines. They offer a cost-effective solution for low to medium voltage transmission systems, ensuring the safety of electrical distribution systems and preventing accidents due to electrical faults. While composite pin insulators and polymer pin insulators provide certain advantages over traditional materials, pin insulators are still a popular choice due to their reliability and ease of use.
In this blog, we will discuss the core advantages, disadvantages, and causes of failure for pin type insulators, along with relevant standards and guidelines, such as IEC 60383 and ANSI C29.5, to provide you with the necessary information for choosing the best solution for your infrastructure.
2. What is a Pin Type Insulator?
A pin type insulator is a type of electrical insulator for power lines that attaches a conductor to a crossarm on a pole. These insulators are typically made of materials like porcelain or polymer, providing electrical insulation to ensure the safe transmission of electricity. Pin insulators come in single-piece or multi-piece insulator designs, with the latter being used for higher voltage applications.
Pin insulators are primarily used for voltages up to 33 kV, and for higher voltages, composite pin insulators or polymer pin type insulators are preferred due to their superior weather resistance and UV resistance. Substation insulators and insulator mounting pins are also commonly used in power stations and substations to maintain safe electrical isolation between conductive parts.
Structure and Design of Pin Insulators
Pin insulators are mounted on crossarms using insulator mounting pins, with the conductor secured in a groove at the top of the insulator. This design provides both electrical conductor support and electrical insulation. For higher voltage systems, multiple pieces of insulators are used to distribute the stress and weight. However, this increases the mechanical load and bending stress on the insulator mounting pin, especially in high-voltage applications.
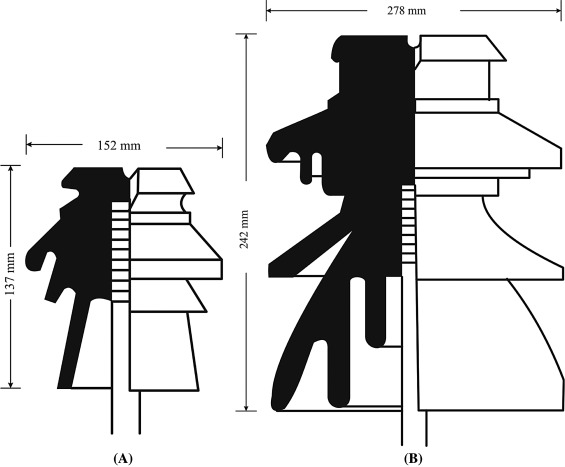
source: ScienceDirect
3. Advantages of Pin Type Insulators
Pin type insulators have been a trusted choice for many years due to their numerous advantages. Let’s explore these in detail.
3.1 Enhanced Safety
Pin type insulators offer high electrical insulation that prevents leakage currents from flowing to unintended parts of the system. This makes them ideal for maintaining high voltage safety and reducing the risk of electrical accidents.
3.2 Reliable Performance
These insulators provide reliable electrical flashover prevention and are designed to withstand mechanical stresses. The combination of mechanical strength and electrical resistance ensures continuous and stable performance in power systems.
3.3 Cost-Effective
Pin type insulators are an affordable solution for electrical power transmission systems, especially for lower voltages. Their simple construction and easy installation make them a budget-friendly option for utility companies and residential power networks.
3.4 Versatility
Pin type insulators are versatile and can be used in various voltage ranges, from 11 kV pin type insulator systems to higher voltage applications. They are compatible with electrical distribution systems, offering flexibility in installation and use.
3.5 Environmental Sustainability
Composite pin insulators and polymer pin insulators are becoming more popular due to their durability and recyclability. These materials offer a more sustainable option, with improved weather resistance insulator properties, allowing them to perform well in extreme conditions.
3.6 Low Maintenance Requirements
Pin insulators, particularly those made from polymer or composite materials, require minimal maintenance. Their self-cleaning ability due to rain and wind helps keep the insulator surface clean, minimizing the need for manual cleaning and reducing long-term operational costs.
4. Disadvantages of Pin Type Insulators
While pin insulators are advantageous, they come with limitations that should be considered in specific applications.
4.1 Limited Voltage Capacity
Pin insulators are most effective for voltages up to 33 kV. Beyond this level, their performance declines, and they are not as effective in handling higher voltages. For high voltage systems, suspension insulators or polymer pin insulators are more suitable.
4.2 Mechanical Stress at Higher Voltages
As the voltage increases, the use of multiple pieces in pin insulators adds weight, which increases the mechanical stress on the insulator mounting pin. This can lead to damage in extreme weather conditions or during heavy mechanical loads.
4.3 Vulnerability to Puncture
In wet conditions, pin type insulators can be susceptible to puncture failure due to the creation of a conductive path when moisture accumulates. This can cause electrical flashover and damage the insulator.
4.4 Potential for Flashover
Under high-voltage conditions, pin insulators may experience flashover, particularly when the creepage distance is insufficient. This is more likely to occur when the insulator is subjected to environmental factors like pollution or moisture.
5. Causes of Insulator Failure
Pin insulator failure can occur due to several factors, each of which can affect the insulator’s performance and longevity.
5.1 High Voltage Stress
Excessive high voltage stress can lead to electrical breakdown or flashover between the conductor and insulator, especially when used beyond their rated voltage capacity.
5.2 Environmental Factors
Pollution, moisture, and weather conditions can accelerate the degradation of pin insulators. In areas with high pollution levels, insulators may experience reduced weather resistance, leading to failure.
5.3 Mechanical Stress
Excessive mechanical load, especially in multi-piece insulators, can lead to damage or failure. This is particularly problematic in high voltage systems where the insulator must bear more weight.
5.4 Aging and Material Degradation
Exposure to environmental elements over time causes aging and material degradation in insulators, which can weaken their mechanical and electrical properties.
5.5 Improper Installation or Maintenance
Incorrect installation or failure to maintain pin insulators regularly can lead to malfunction. Ensuring proper installation and periodic inspection is crucial for the long-term performance of pin insulators.
6. Common Standards for Pin Type Insulators
Pin type insulators must comply with industry standards to ensure reliability and safety. Some of the key standards include:
-
IEC 60383 – Standard for porcelain insulators for overhead lines.
-
ANSI C29.5 – Standard for porcelain pin insulators used in electrical transmission systems.
-
IEC 61109 – Standard for polymer insulators.
-
IS 731:1971 – Standard for pin type insulators in India.
-
IS 2486 – Indian standard for insulators.
These standards ensure that pin type insulators meet the required creepage distance, mechanical strength, and safety parameters.
7. When to Use a Pin Type Insulator?
Pin type insulators are best suited for low to medium voltage applications, particularly in the following cases:
-
Electrical distribution networks where voltage does not exceed 33 kV.
-
Residential and rural power systems that require cost-effective and reliable insulation.
-
Areas with moderate environmental conditions where self-cleaning properties can function effectively.
For high voltage systems, suspension insulators or polymer pin insulators are recommended due to their better performance under high stress.
8. Conclusion
Pin type insulators are a reliable and cost-effective solution for low to medium voltage power systems. With their durable performance, low maintenance, and versatility, they remain an excellent choice for many electrical transmission applications. However, for higher voltage transmission lines, other types of insulators, such as suspension insulators, should be considered for optimal performance.
When choosing an insulator, it’s important to assess the voltage requirements, environmental conditions, and mechanical stresses to ensure the best insulator for your electrical system.
FAQs About Pin Type Insulators
What is the maximum voltage for pin insulators?
Pin insulators are typically used for voltages up to 33 kV. Beyond this, suspension insulators or polymer pin insulators are preferred.
Why are pin insulators not used for higher voltages?
Pin insulators are not suitable for higher voltages because they cannot handle the additional mechanical and electrical stress. Suspension insulators are better suited for high-voltage applications.
What causes pin insulators to fail?
Failure can result from high voltage stress, environmental factors, mechanical stress, aging and material degradation, and improper installation.
How can I maintain pin insulators?
Regular inspections for wear, cleaning to prevent pollution buildup, and ensuring proper mechanical load distribution are crucial for maintaining pin insulators.