Bimetallic lugs—also known as Al Cu lugs—play a vital role in ensuring reliable and safe cable termination, especially when connecting aluminum conductors to copper busbars or terminals. Whether you’re working in power transmission, automotive wiring, or renewable energy systems, these hybrid connectors minimise electrochemical corrosion and maintain long-term conductivity. In this article, we’ll explore the practical applications of bimetallic cable lugs, walk through the correct installation process, and share expert insights from a professional cable lugs manufacturer to help you achieve safe and efficient connections across various industries.
Application
1.Power transmission and distribution system: Bimetallic lugs are widely used in power transmission and distribution systems, especially at overhead cables or cable connections. Bimetallic lugs can connect cables firmly and durable, ensure the normal transmission of current, reduce the risk of electrical failures caused by poor contact or corrosion, and improve the reliability and safety of power transmission and distribution systems.
2.Automotive industry: Bimetallic lugs play an important role in the electrical systems of the automotive industry. They are widely used in various electrical connections in automobiles, including but not limited to battery line connections, sensor connections, lighting system connections, and power connections for on-board electronic devices. They can provide stable electrical connections, and bimetallic lugs can reduce electrochemical corrosion caused by contact between different metals while ensuring low impedance and high conductivity. The use of such lugs improves the reliability and life of automotive electrical systems. At the same time, the automotive industry has very high requirements for safety and durability. All components must adapt to high-strength and high-vibration environments, and bimetallic lugs can meet these requirements at the same time, so they have become an indispensable component in automotive electrical systems.
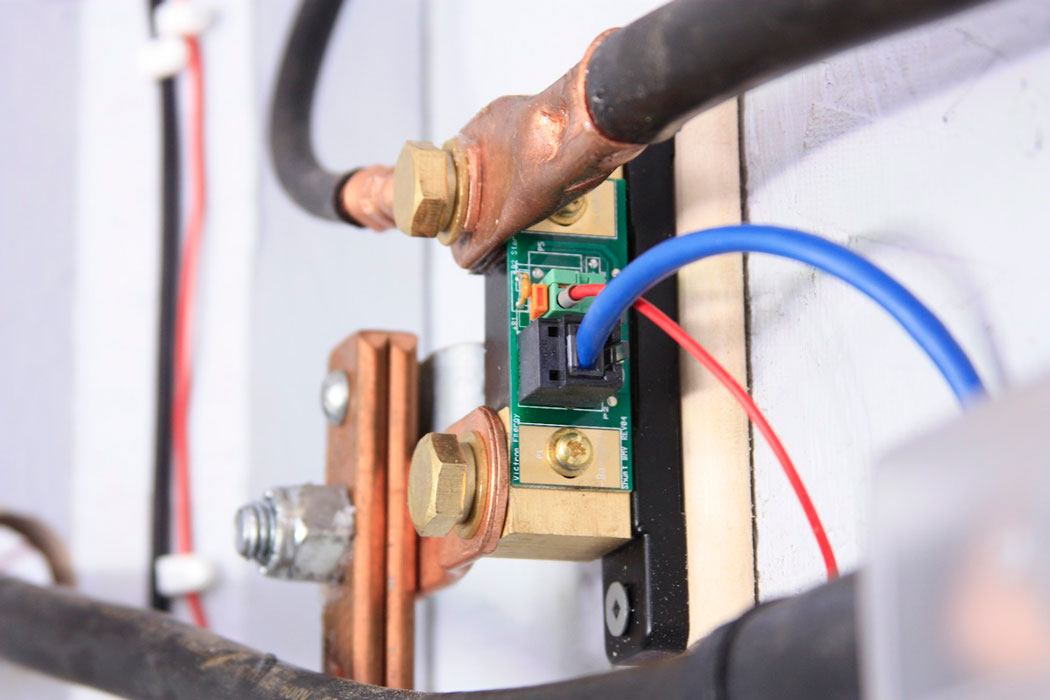
copper lugs Application
3. New energy industry: The application of bimetallic lugs in the new energy industry is mainly reflected in their excellent conductivity and durability. For example, in wind power generation or solar photovoltaic power generation systems, when cables made of bimetallic lugs are connected to electrical equipment, their unique circular terminals can expand the contact area, reduce energy loss, and can also withstand large currents. Therefore, they are most widely used in energy storage systems and inverters in new energy.
4.Marine industry: The application of bimetallic lugs in the marine industry mainly utilizes their excellent corrosion resistance and excellent electrical connection reliability. In the marine environment, the air is humid and salty, so extremely high requirements are placed on the corrosion resistance of electrical connection materials. The bimetallic design of the bimetallic lug can effectively prevent electrochemical corrosion from destroying the connection between the lug and the cable in the high-salt, highly corrosive environment of seawater, maintain reliable connection between the cable and the connector, the electrical connector and the equipment, reduce maintenance costs and extend service life.
5.Industrial industry: Bimetallic lugs are indispensable in the entire production and manufacturing process of industrial production. Due to their unique structural design, the lugs are made of metals with different thermal expansion coefficients, which allows the lugs to expand and contract as needed without losing their conductivity or mechanical integrity. They can maintain performance under extreme temperatures and high electrical loads. They play a key role in ensuring the stability of electrical connections, improving energy efficiency and enhancing equipment performance.
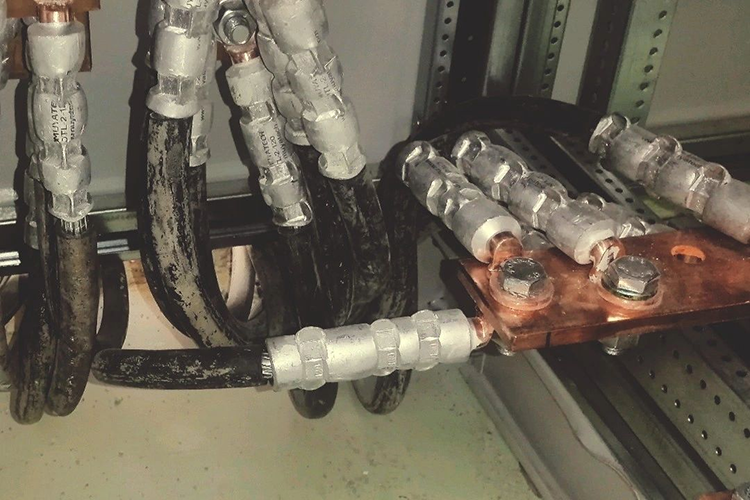
DTL 2 Bimetallic Lugs Application
Installation
The installation process of bimetallic lugs requires specific steps to ensure safety and reliability. Precise torque control and correct crimping techniques are required during the installation process to ensure long-term reliability and performance. The following are the specific steps for their installation:
1. Preparation: Before installation, check the bimetallic lugs model, and it is recommended to lightly polish the conductor surface to remove the oxide layer and dirt, improve contact and ensure good electrical connection. Then check whether the tools required for installation are complete.
2.Wire stripping: Peel the outer skin of the wire to be installed to expose the inner core for the next step of installation.
3 Insert the wire: Insert the stripped wire into the hole of the bimetallic lug, and ensure the depth of the wire insertion, ensure that the stripped wire part can be fully inserted into the hole of the lug, and let the wire and lug fully contact.
4. Crimping process: Hold the crimping pliers handle with your hand, slowly apply pressure, make sure the pressure is moderate, press the aluminum wire and copper wire tightly together, and after crimping, gently pull the wire to check whether the wire is completely crimped and secure.
5.Protective treatment: This step is essential. After crimping, apply special protective materials, such as conductive anti-corrosion paste, or wrap the joint with insulating tape or heat shrink tube. After these protective treatments, the oxidation resistance of the terminal piece can be further improved and the service life can be extended.
6.Torque control: When installing the terminal block to the equipment or busbar, it is recommended to use self-breaking screws (torque disconnection) when tightening the terminal block. This only needs to be tightened with a wrench. Because when the tightening torque (7 to 10 Nm) is reached, the screw head will break off, which ensures that the correct torque is always used.
7. Inspection and testing: After all these are completed, finally check whether the entire wiring lug is firmly connected and whether the terminal contact is good. If everything is normal, a power-on test is required to observe whether the line current and voltage using the wiring lug are stable.
Summary
Bimetallic lugs provide a reliable solution for electrical connections. They have good resistance to electrochemical corrosion, long service life, and good electrical conductivity. They are widely used in various industries. At the same time, correct installation steps are the basic guarantee to ensure that bimetallic lugs can perform their performance, especially the protective treatment after installation, which is often overlooked by many people.
FAQS
Q: Why use bimetallic lugs?
A: Bimetallic lugs have good resistance to electrochemical corrosion, long service life, good conductivity, etc., and can adapt well to various environments, which ordinary metal lugs cannot do.
Q: What is the electrochemical corrosion mentioned in this article? How to prevent and control it?
A: Electrochemical corrosion refers to the galvanic reaction that occurs when impure metals come into contact with electrolyte solutions, in which the more active metals lose electrons and are oxidized. Electrochemical corrosion can be reduced by covering with protective layers, such as protective films, heat shrink tubes, etc.
Q: How to choose copper lugs?
A: Consider the cable size, current rating, installation environment, and lug type (e.g. ring, pin, or tubular). For a detailed guide, check out our blog on how to choose the best copper lugs.
Through this article, you can learn in detail about the specific application and correct installation steps of bimetallic lugs, which can effectively improve the reliability of your electrical connections. If you want to know more about bimetallic lugs, you can directly visit SUNJ website or contact our professional engineers to get solutions.