Introduction
In electrical distribution systems, making safe and reliable connections is crucial to maintaining efficiency and minimizing downtime. One of the most innovative solutions for this is the IPC Insulation Piercing Connector. Designed to penetrate the insulation of a cable without stripping, it provides a secure, low-resistance connection while preserving the conductor’s integrity. This article explores how IPC connectors work, their advantages over traditional crimp connectors, their various applications, installation methods, and key industry standards.
What Is an IPC Insulation Piercing Connector?
IPC Insulation Piercing Connectors are devices that create electrical connections between main power cables and branch conductors without stripping insulation. They have sharp metallic teeth that pierce the insulation, ensuring direct metal-to-metal contact while keeping the cable’s protective outer layer intact.
These connectors are widely used in low-voltage and medium-voltage power distribution networks. They are essential in aerial bundled cables (ABC), street lighting, and residential power connections. Their ability to support aluminum and copper conductors makes them a versatile choice across different electrical infrastructures.
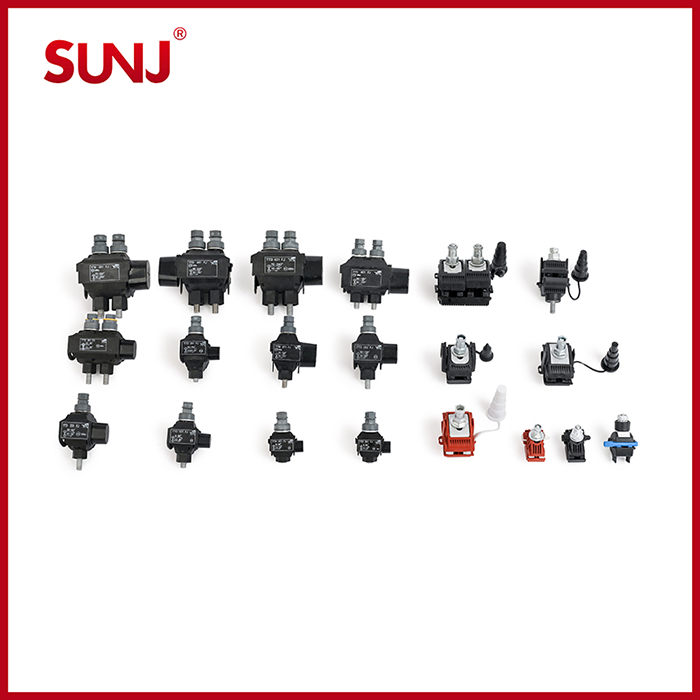
Ipc Insulation Piercing Connector
How Does an IPC Connector Work?
The core mechanism behind an IPC Insulation Piercing Connector lies in its self-piercing design. When the connector is tightened, the internal blade teeth press into the conductor, cutting through the insulation without causing significant damage to the cable. This process forms a conductive interface that allows electricity to flow efficiently.
Most IPC connectors incorporate a shear-head bolt mechanism, which ensures that the correct torque is applied during installation. Once the bolt reaches the required tension, the head automatically shears off, preventing over-tightening and securing a consistent electrical connection.
Waterproof sealing components are often integrated into IPC connectors, enhancing their durability in outdoor and underground installations. These features prevent moisture ingress and oxidation, making IPC connectors highly resistant to environmental wear and corrosion.
Components of an IPC Insulation Piercing Connector
An IPC Insulation Piercing Connector is composed of several essential elements that work together to ensure a reliable connection.
Shear-head bolt: Ensures the correct torque is applied, preventing over-tightening.
Blade teeth: Made of corrosion-resistant metal, they pierce the insulation to establish a secure contact with the conductor.
Upper and lower body: Designed to provide insulation and mechanical protection.
Waterproof sealing: Protects against moisture, enhancing longevity in harsh environments.
Stainless steel washer: Adds structural integrity and prevents rusting.
End cap: Provides additional insulation at the cable end to maintain safety.
Each of these components plays a critical role in ensuring that the connection remains secure, conductive, and long-lasting, even under extreme weather conditions.
Advantages of IPC Connectors Over Traditional Crimp Connectors
Compared to traditional crimp connectors, IPC Insulation Piercing Connectors offer a range of benefits that make them a superior choice in many applications.
Time efficiency: Traditional crimp connectors require stripping the insulation, crimping the connector, and applying insulation tape. IPCs eliminate these steps, reducing installation time.
Enhanced safety: Since IPC connectors do not require insulation stripping, the risk of accidental conductor damage or electric shock is minimized.
Waterproof and corrosion-resistant: The sealing mechanisms ensure long-term durability, making them ideal for outdoor applications.
Consistent torque application: The shear-head bolt design guarantees a uniform and optimal connection pressure, reducing the risk of poor electrical contact.
Compatibility: IPC connectors are suitable for aluminum-to-aluminum, copper-to-copper, and aluminum-to-copper connections, whereas traditional crimp connectors often require additional compatibility considerations.
Space efficiency: Their compact design allows for easy integration into power grids with limited space.
These advantages make IPC connectors the preferred choice in many modern power distribution projects.
Top 6 Applications of an IPC Insulation Piercing Connector
IPC connectors are widely used across multiple industries and electrical applications due to their adaptability and efficiency.
Street Light Connections
One of the most common applications of IPC connectors is in street lighting systems. They allow quick and secure branching from main power lines to individual streetlights, ensuring a consistent power supply.
Tap-off/Multi-Tap Connection to Households
IPC connectors play a crucial role in residential electricity distribution. They enable direct connections from aerial bundled cables to homes, making it easier to expand power networks without extensive cabling modifications.
Distribution Box Charging Connection
In low-voltage distribution systems, IPC connectors help facilitate reliable power transfer to distribution boxes, ensuring steady electrical flow for multiple circuits.
Jumper Connection
Jumper connections require secure and low-resistance links between two cables of the same size. IPC connectors provide an efficient solution for T-connections and high-angle turns in electrical networks.
Automotive Systems
In the automotive industry, IPC connectors are used in wiring harnesses, battery connections, and sensor integrations, ensuring stable electrical connections without extensive modifications.
Insulation Piercing Connector for ABC Cable
IPC Insulation Piercing Connectors are crucial in Aerial Bundled Cables (ABC), widely used in modern power distribution networks for their safety, efficiency, and ease of installation. These connectors enable secure, reliable, and maintenance-free branch connections by piercing the cable insulation without the need for stripping, enhancing installation speed and reducing maintenance needs. As a leading manufacturer, we offer high-quality insulated piercing connector for abc cable solutions, ensuring optimal performance and longevity in various electrical systems.
Screw-Type vs Spring-Loaded IPCs
When selecting an IPC Insulation Piercing Connector, understanding the differences between screw-type and spring-loaded variants is crucial. Below is a detailed comparison based on six key dimensions:
Feature | Screw-Type IPCs | Spring-Loaded IPCs |
Installation | Requires a tool to tighten the shear-head bolt, ensuring precise torque and a secure connection. | Uses internal spring tension to pierce and hold the conductor, allowing faster, tool-free installation. |
Connection Strength | Highly stable and rigid, ideal for long-term installations. | Less rigid, may loosen over time due to spring fatigue. |
Cost Consideration | Higher upfront cost, but better long-term reliability. | Lower initial cost, but may require more frequent replacements. |
Torque Control | Shear-head bolts prevent over-tightening, ensuring consistent pressure. | Spring tension varies, which may lead to inconsistent contact pressure. |
Durability & Lifespan | Extremely durable, resistant to vibration and movement, ideal for harsh environments. | May degrade as the spring loses elasticity, requiring periodic checks. |
Best Use Cases | Suitable for permanent installations, overhead networks, and street lighting where reliability is key. | Ideal for quick installations, testing applications, and temporary power setups. |
Environmental Resistance | Stronger sealing against moisture and corrosion, better for outdoor use. | Still weather-resistant but may have weaker sealing. |
Which One Should You Choose?
For long-term stability and harsh environments, go with screw-type IPCs.
For quick installation and flexibility, choose spring-loaded IPCs.
The right choice depends on your installation needs, environmental conditions, and maintenance expectations.
How Do You Install an IPC Insulation Piercing Connector?
Proper installation of an IPC Insulation Piercing Connector ensures a secure and long-lasting electrical connection. Following the correct procedure reduces the risk of connection failure and enhances system reliability.
Installation Steps
1.Preparation
Identify the main cable and branch cable that will be connected.
Ensure that the IPC connector is compatible with the conductor sizes and material (aluminum or copper).
Inspect the IPC and cables for any visible defects before installation.
2.Positioning
Place the main cable into the designated groove of the IPC.
Insert the branch cable into the secondary groove to ensure proper alignment.
Verify that both cables are properly positioned without twisting or overlapping.
3.Pre-Tightening
Lightly tighten the bolts by hand to secure the cables in place.
Ensure that the cables are firmly seated within the IPC without excessive movement.
Double-check alignment to prevent improper piercing during the next step.
4.Piercing the Insulation
Use a torque wrench or the appropriate tightening tool.
Gradually tighten the IPC bolts according to the recommended torque settings to ensure proper piercing.
Continue tightening until the shear-head bolt snaps off, indicating that the optimal torque has been reached.
Avoid over-tightening, as it may damage the conductor.
5.Inspection & Verification
Visually inspect the IPC to confirm there are no gaps between the connector and the cables.
Check that the bolts are properly sheared, leaving a flush and secure connection.
Lightly tug both cables to ensure they are firmly held in place.
6.Sealing and Protection
Verify that the self-sealing waterproof mechanism is engaged, protecting the connection from moisture and corrosion.
If applicable, apply additional insulation covers or protective coatings for extreme environmental conditions.
Ensure the IPC is securely fastened to prevent vibration-related loosening.
Installation Considerations
Avoid installation in heavy rain or extreme cold, unless the IPC is specifically rated for such conditions.
If used outdoors, ensure the IPC has UV-resistant properties to prevent degradation.
Regularly inspect IPC connections for any signs of corrosion, loosening, or wear.
Perform periodic maintenance and re-tighten connections if necessary to maintain long-term performance.
Following these guidelines ensures a durable and efficient IPC connection, minimizing the risk of failure while optimizing electrical performance.
How to Test Performance of IPCs?
The reliability of an IPC connector is determined through rigorous testing procedures. Some of the most common tests include:
Dielectric voltage test in water: Evaluates insulation resistance under wet conditions.
Corrosion resistance test: Assesses long-term exposure to environmental elements.
Mechanical strength test: Measures the connector’s ability to withstand external forces.
Short circuit endurance test: Determines performance under high electrical loads.
By passing these tests, IPC connectors demonstrate their reliability in real-world applications.
Industry Standards & Certifications
Ensuring compliance with industry standards is essential for safe and efficient electrical installations. IPC connectors typically adhere to the following certifications:
IEC 61238-1-2: Covers mechanical and electrical durability.
BS EN 50483-4: Specifies test requirements for low-voltage ABC cable accessories.
NFC 33-020: French standard for insulation piercing connectors in power networks.
These certifications confirm the quality, durability, and safety of IPC connectors in various electrical applications.
How to Choose an IPC Connector?
Selecting the right IPC connector depends on various factors, including:
Cable material and size compatibility
Environmental conditions (outdoor, underground, marine, etc.)
Voltage and current capacity
Installation method and ease of use
Ensuring that the chosen IPC meets project-specific requirements is key to long-term performance and reliability.